Demystifying plastic types – How to navigate the complex web of seemingly eco-friendly plastics
Most consumers already know that the global status of plastic as the go-to packaging material has detrimental effects on nature. The problems with traditional plastics have spawned various solutions that are marketed as environmentally friendly alternatives to traditional petroleum-based plastic. These alternatives, however, vary greatly in their properties and require conscious consumers and legislators to stay vigilant.
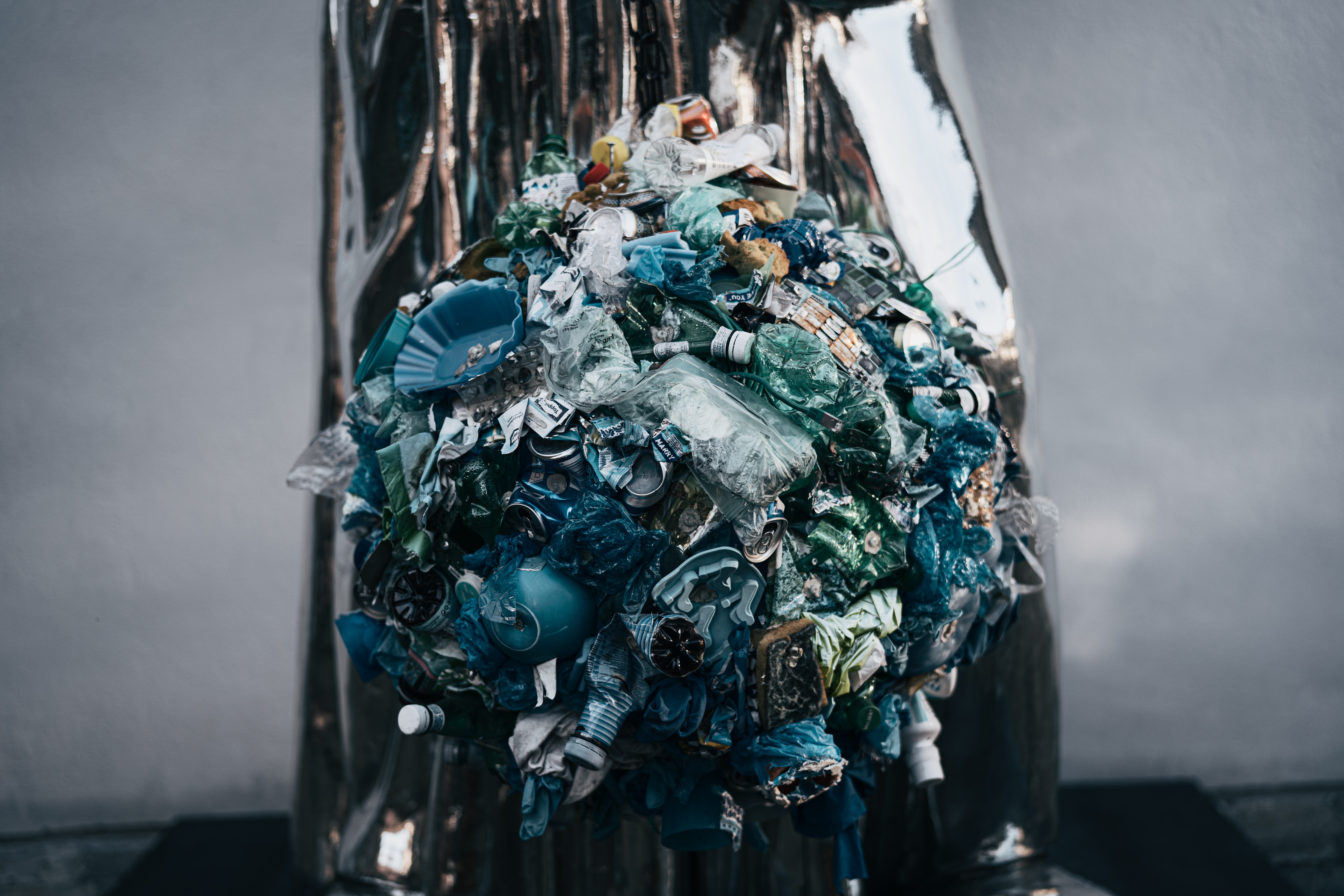
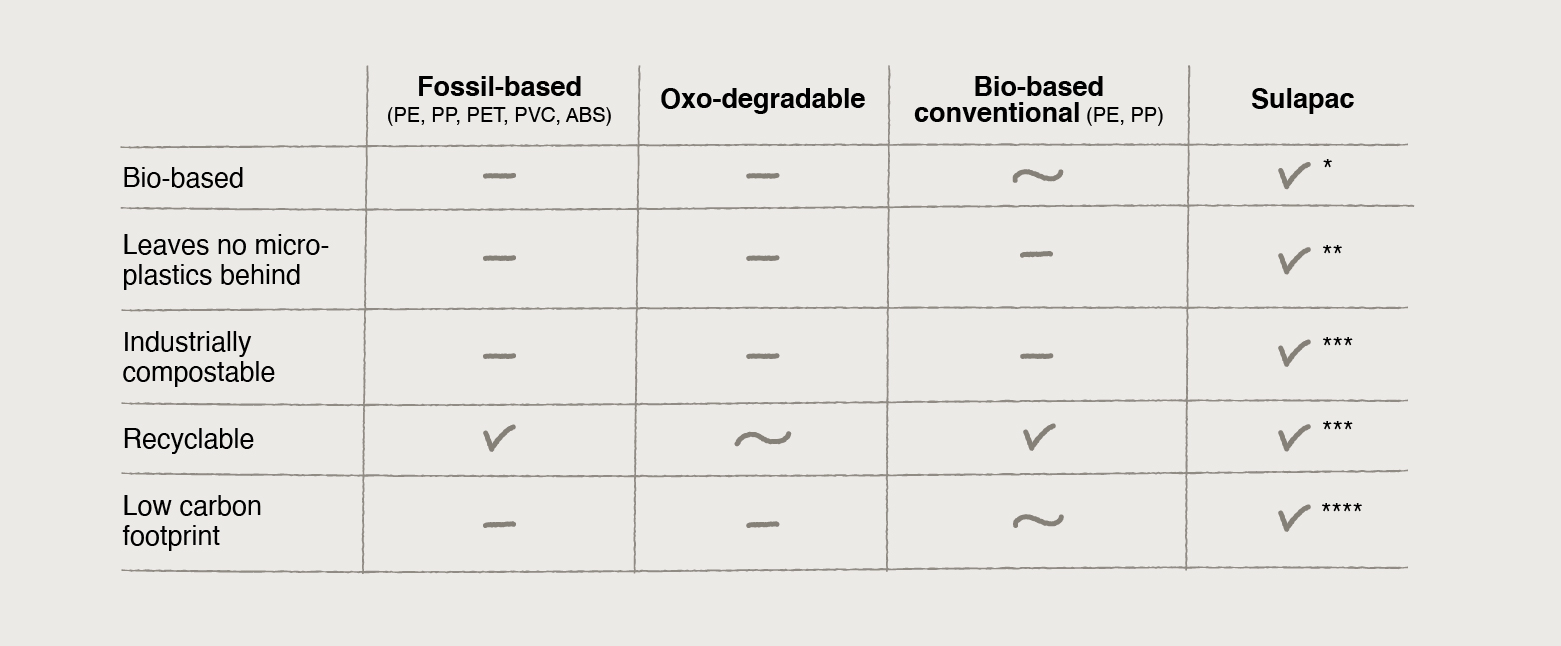
Fossil-based plastics (PE, PP, PET, PVC, ABS)
Definition: Fossil-based plastics are polymers that are made of petrochemicals. Fossil-based plastics come from non-renewable sources.
Products: As all plastic was originally fossil-based, the range of different products is enormous. Most fossil-based plastics are used as packaging material. There are, however, also extremely durable plastics that are used in construction and the automobile industry, for example.
Pros: Because of volume, conventional, fossil-based plastics offer an affordable solution for prolonging the shelf life of many products, especially food. Their durability and lightness can make them a more eco-friendly alternative for many metals.
Cons: Fossil-based plastics are permanent. They don’t biodegrade in nature but still release harmful microplastics that then circulate in the ecosystem.
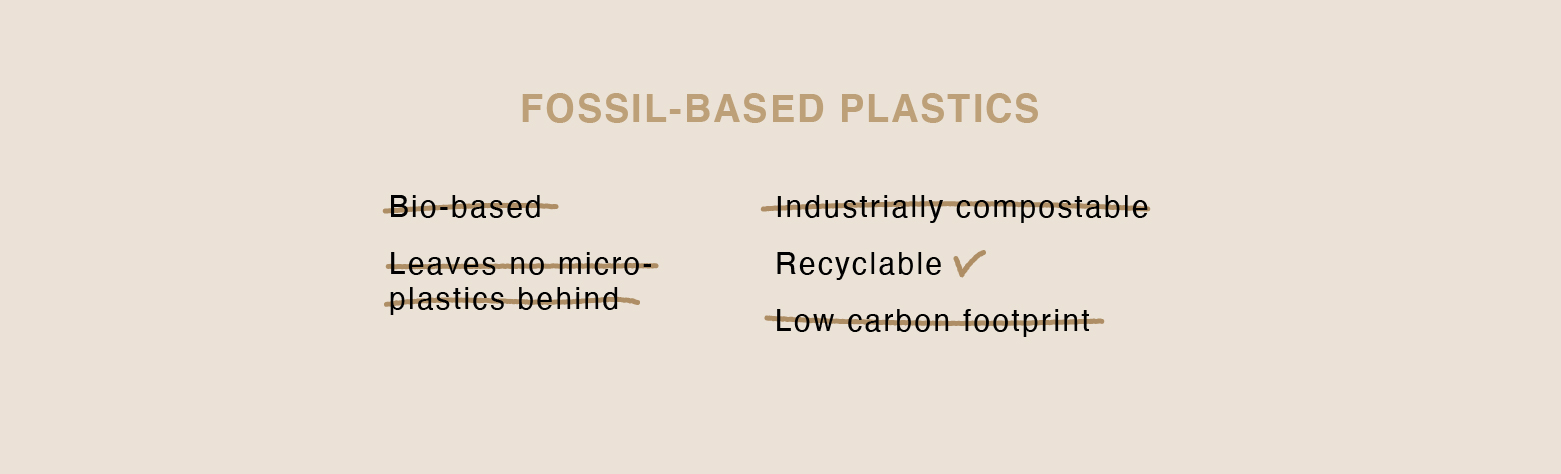
Oxo-degradable plastics
Definition: Oxo-degradable plastics combine bio-based materials with fossil-based polymers. As a result, the plastic breaks down and circulates in the ecosystem but doesn’t biodegrade.
Products: Plastic bags, short-term single-use products such as food package films.
Pros: None.
Cons: Oxo-degradable plastics can be labeled as greenwashing, since they fragment but don’t biodegrade, resulting in major microplastics release. You get better durability properties with fossil-based plastic. Oxo-degradable plastics are also hard to recycle and can even disturb the operation of recycling facilities as the fast-degrading shreds sometimes block machines.
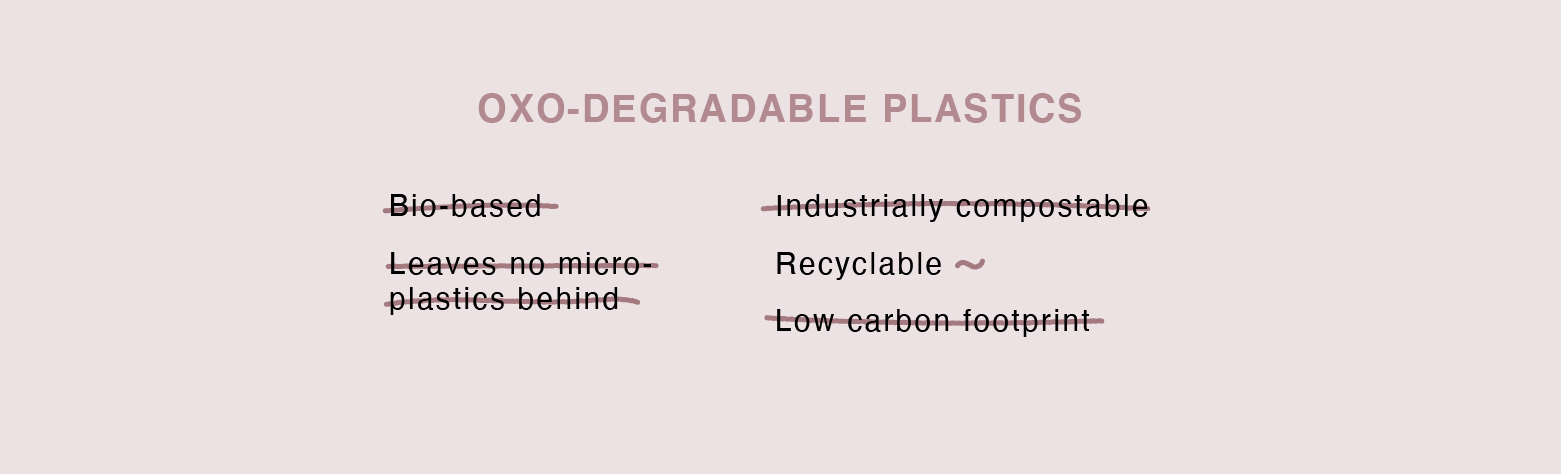
Bio-based conventional plastics
Definition: Bio-based conventional plastics are plastics made from renewable sources, yet they don’t biodegrade. Instead of relying on petrochemicals, bio-based conventional plastics utilize organic products, such as palm oil or pine oil. Both fossil- and bio-based processes, however, result in the same polymers, such as PP or PE, which are conventional plastics. Hence, they are permanent.
Products: Since bio-based production largely uses the same polymers as fossil-based processes, you can also make similar products regardless of the process.
Pros: When you make plastic from organic industry side streams, for example, the carbon footprint is smaller than with fossil-based, non-renewable ingredients.
Cons: Some legislations allow products to be classified as bio-based even if they contain only 20% of bio-based raw materials. What’s more, the word bio doesn’t guarantee that the product is sustainable, although it is often greenwashed to seem eco-friendly. Bio-based conventional plastics are still PP and PE and have the same properties. They also have the same detrimental effects on nature as their fossil-based counterparts: they all release permanent microplastics.
Unfortunately, there is also a wider negative effect on nature due to the high demand of bioplastics. Rainforests are cut down to make room for crop that is better suited for plastic production.
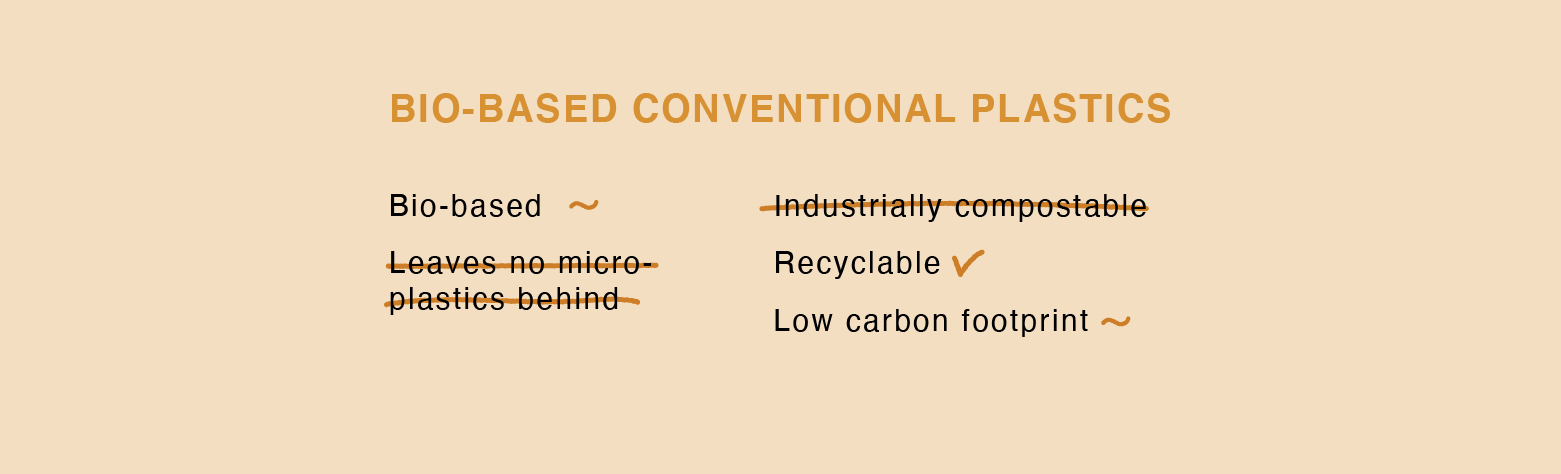
Sulapac
Definition: Sulapac is a beautiful and functional bio-based material that is designed to mimic nature. We utilize responsibly sourced, sustainable raw materials, such as industrial and agricultural side streams. Sulapac biodegrades without leaving permanent microplastics behind.
Products: Sulapac is suitable for various applications, including food contact products, cosmetics and luxury packaging.
Pros: Sulapac biodegrades fully without leaving permanent microplastics behind. Utilizing industry and agriculture side streams reduces Sulapac’s carbon footprint, and the material can be processed with existing plastic product machinery. Every step of the value chain, from raw material sourcing to end of life, is carefully considered from a sustainability point of view.
Just recently, we piloted a take-back program that aims to save nature’s resources and lower the carbon footprint even further. Circular economy is at the heart of our operations. Also, the Sulapac material has a unique look and feel thanks to our special combination of raw materials. It is a wow factor for premium brands.
Cons: Sulapac’s production costs are currently slightly higher compared to traditional plastic because of production volume, but increased demand is making Sulapac more affordable by the day. At the moment, some production methods aren’t suitable for Sulapac, which reduces the range of potential end products. However, we are continuously developing our materials and processes. More innovation announcements can be expected in the near future.
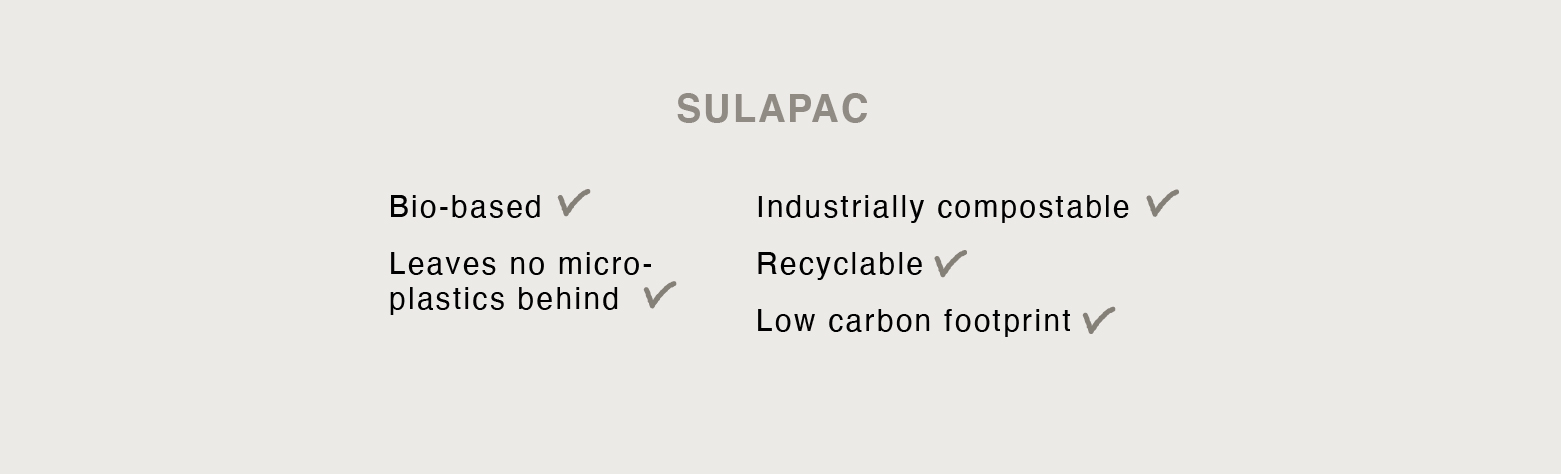
Choosing the right type of plastic does make a difference
As the infographic and descriptions suggest, the choice of plastic really does have an impact, especially on the carbon footprint and microplastics release. In our next blog post about plastics, we’ll address a major problem with plastic – recycling. Plastic production volumes are on the rise, and we still lack adequate global recycling systems for plastics. Using bio-based materials that leave no permanent microplastics behind, such as Sulapac, is becoming increasingly vital for our planet.
You can learn more about our Sulapac® material here.
Jari Salo
Technical Support Manager
Jari Salo is an experienced packaging professional with strong expertise in the packaging, consumer goods and supply industries. Having worked at companies such as Huhtamäki and Paccor, Salo has become an expert in plastic quality control management and R&D. Salo specializes in thermoforming, injection molding, blow film, Flexo-, dry offset- and tampo printing and food safety legislation.