How the PPWR is reshaping packaging—and why Sulapac is leading the charge
The upcoming Packaging and Packaging Waste Regulation (PPWR) is set to redefine packaging across Europe, making recyclability non-negotiable. This landmark regulation will impact every industry player, from manufacturers to brands, so getting to know it is crucial. For forward-thinking companies like Sulapac and its customers, it’s an opportunity to lead the way toward a greener future.
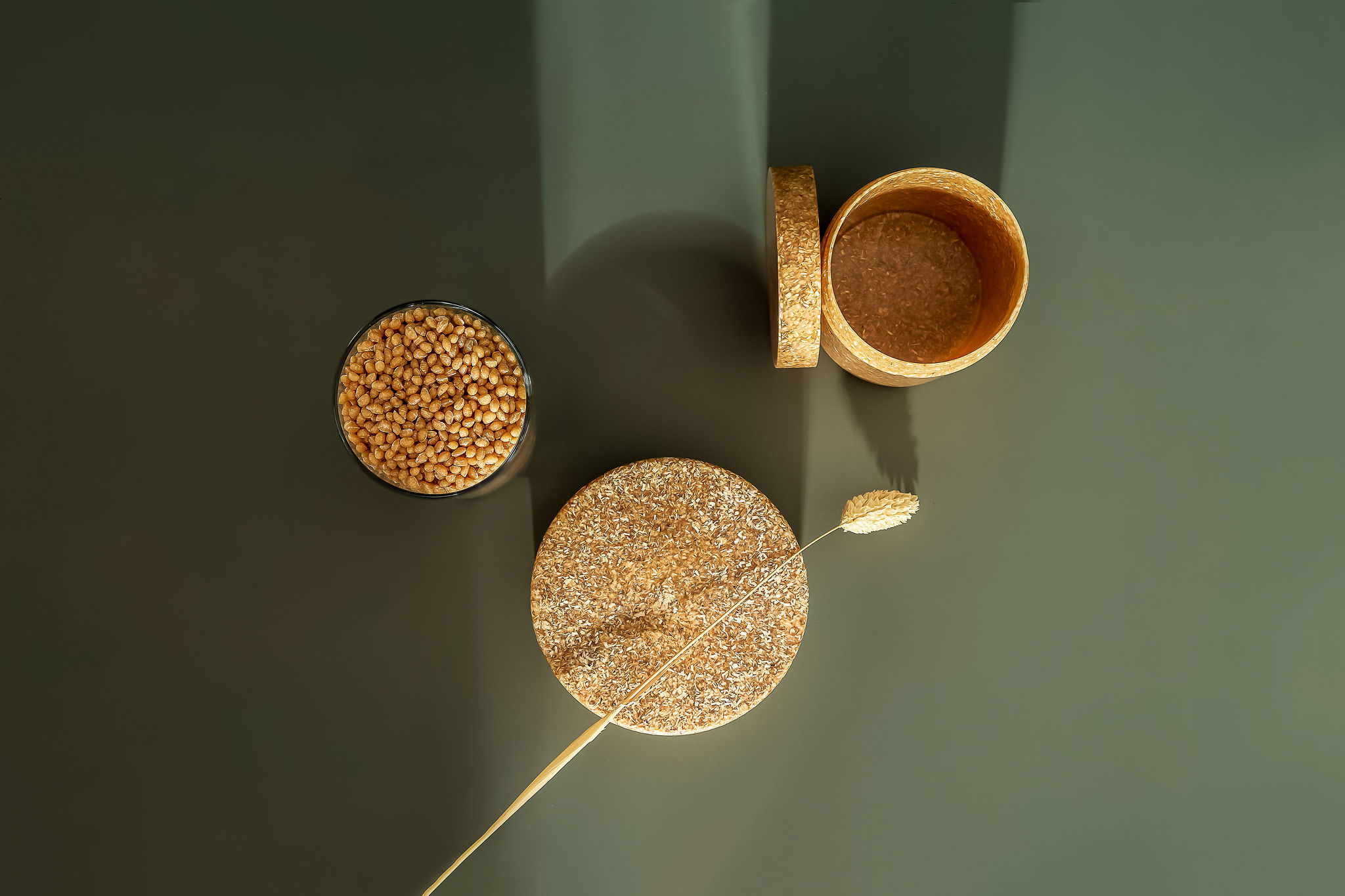
The new PPWR, expected to come into force in the next few years, represents a significant leap in reducing packaging waste and promoting a circular economy. With stringent requirements on recyclability and the use of recycled content in packaging, this regulation will transform packaging design and manufacturing.
To shed light on these upcoming changes, we sat down with Dr. Laura Tirkkonen-Rajasalo, Sulapac’s Chief Compliance Officer and co-founder. She walked us through the latest PPWR updates and shared how a knowledgeable partner can help you stay ahead of compliance.
All packaging must be recyclable by 2030
The big goal of the PPWR? To make all packaging recyclable by 2030. Yes, you heard us right, all packaging, with only very limited exceptions. European lawmakers are currently ironing out the legal details. Although the specifics haven’t been finalized, the direction is clear: businesses will need to adopt recyclable materials. As Laura points out, “It’s a very positive change. The PPWR truly promotes a circular economy for all materials across Europe.”
A key aspect of the PPWR is the introduction of Design for Recycling (DfR) guidelines for different packaging materials. By 2030, all packaging must be compatible with existing collection and recycling systems, and materials will be graded based on their recyclability as A, B, or C.
By 2038, all packaging materials must be rated A or B to be considered recyclable, with grade C no longer accepted. And this is just the beginning—criteria will only get stricter over time.
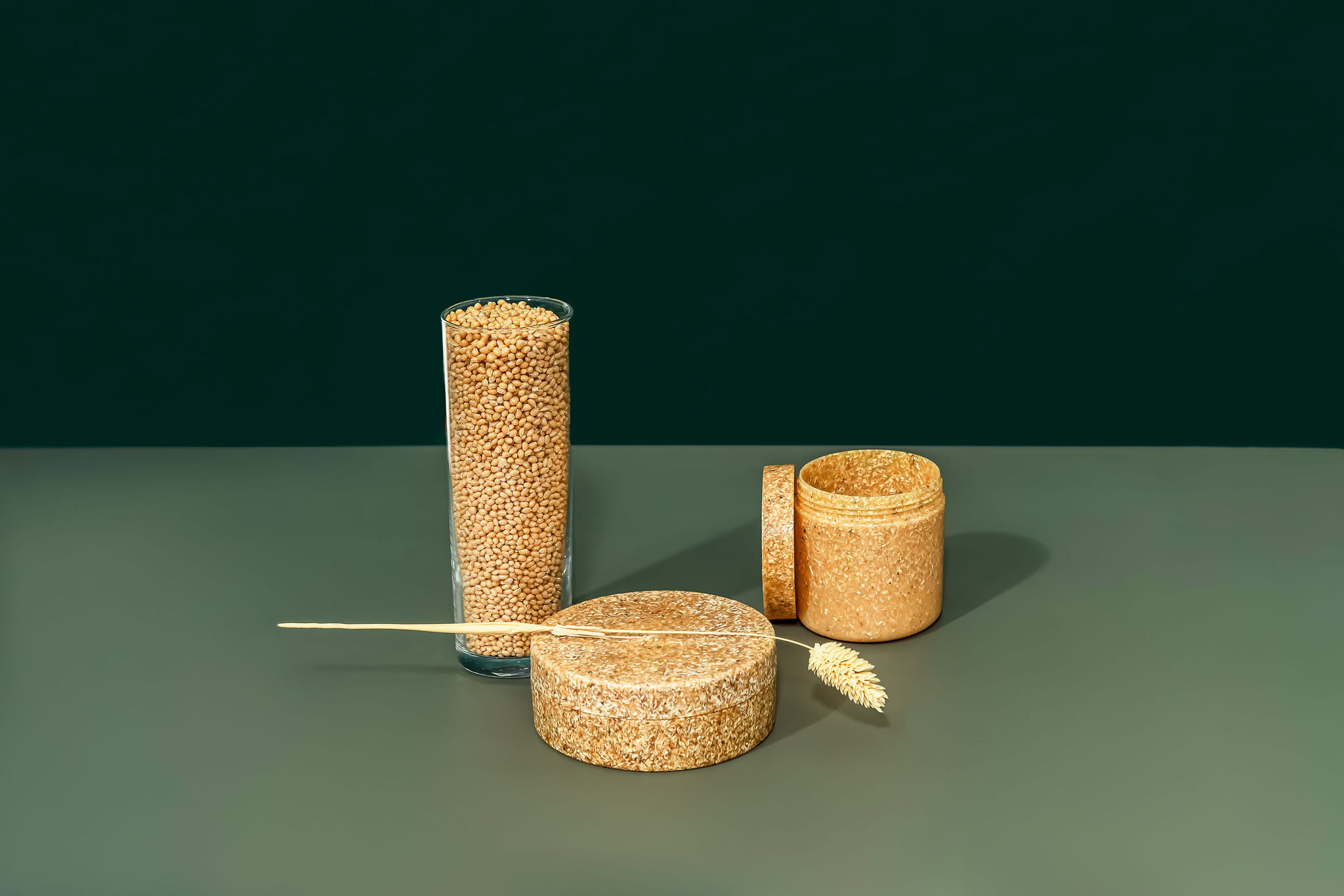
All packaging must be recyclable at scale by 2035
By 2035, in addition to meeting the DfR guidelines, all packaging must be recyclable at scale. “By ‘recyclable at scale’, the PPWR means that the material must be recyclable across Europe in high enough quantity. It’s not enough to have a few closed-loop collections in some locations,” Laura explains.
“At scale” refers to an annual quantity of recycled material equal or greater than 55% for most materials. However, Commission will set many of the details in the coming secondary legislation through the implementing and delegated acts, including details on design for recycling criteria and a methodology for the recycled at scale assessment.
Biodegradable materials recognized as recyclable by the PPWR
Packaging materials produced from bio-based and biodegradable polymers have been recognized as recyclable under the PPWR, marking an important step toward a sustainable circular bioeconomy.
“Sulapac played a key role in advocating for a separate category for biodegradable materials in the packaging category list in Annex II of PPWR, which was indeed added. We are actively involved in various EU-level working groups and associations where bioplastics manufacturers and other stakeholders collaborate to develop industry guidelines for DfR criteria. By participating in these discussions, we can help shape the guidelines and standards that set the recyclability criteria for biodegradable materials, and also make sure our own materials comply,” Laura says.
This involvement ensures that global brands using Sulapac materials in their packaging will meet the requirements of the PPWR and other relevant EU regulations.
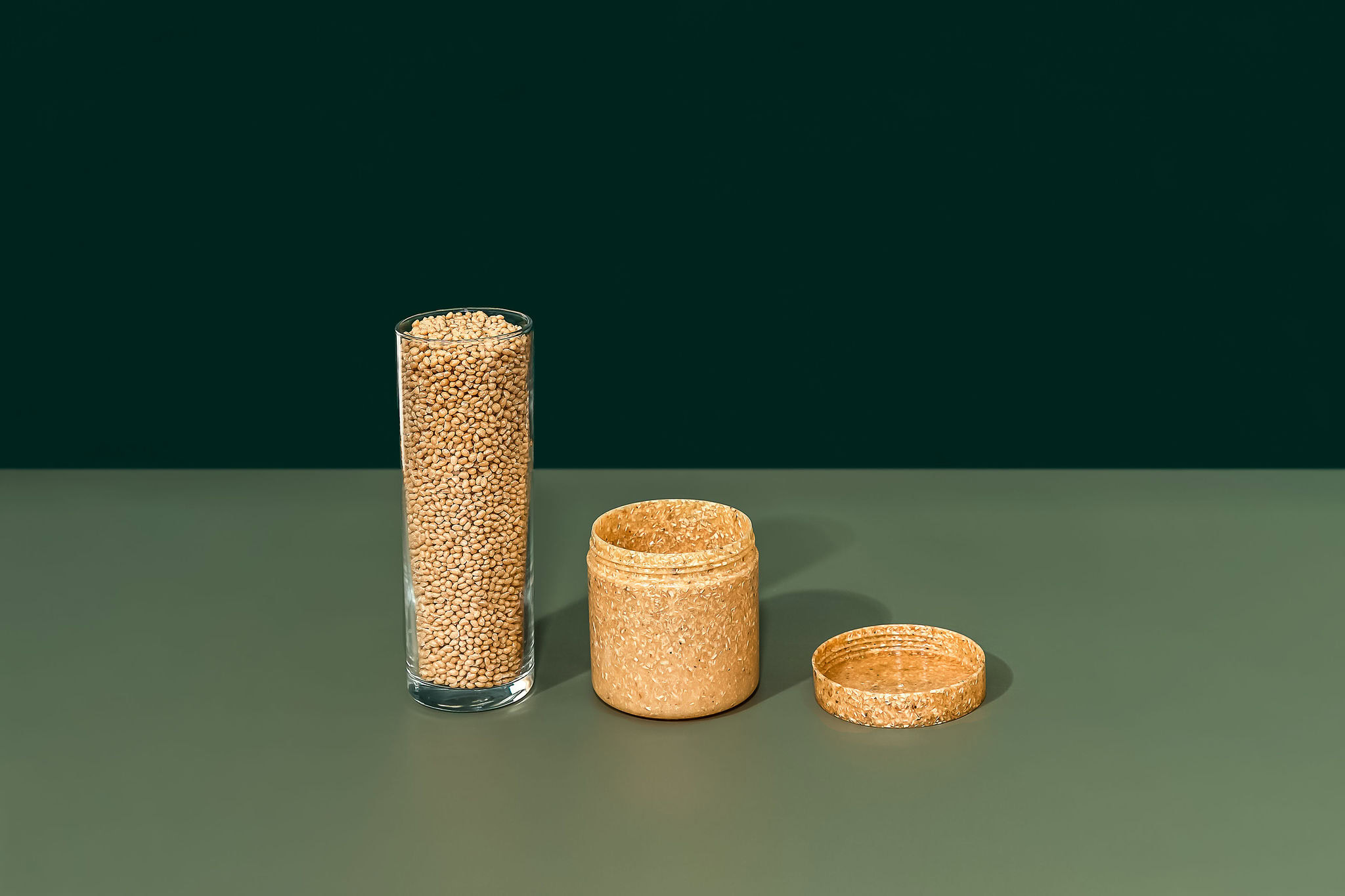
A pathway to becoming recyclable at scale
While large-scale recycling won’t be fully realized until the use of biodegradable materials becomes more mainstream, Sulapac’s materials have already been technically validated for sorting and recycling at scale.
“We have demonstrated that Sulapac materials can be recycled effectively at scale. Chemical recycling plants for similar biodegradable materials already exist, and waste can be sorted efficiently. We are involved in an EU-wide project, ReBioCycle and collaborate with other manufacturers and chemical recyclers to develop a system with the needed infrastructure that supports the widespread adoption and recycling of biodegradable materials,” Laura clarifies.
How do Sulapac materials circulate?
- Collection
Sulapac materials can be collected through existing plastic recycling streams. Tests show that near-infrared (NIR) technology can sort these materials with around 95% efficiency. Biodegradable materials have a distinct spectral signature, differentiating them from traditional plastics.
- Chemical recycling
After being separated, the biodegradable materials are sent to recycling facilities. While mechanical recycling is an option, it often results in quality degradation. For Sulapac’s biodegradable materials, chemical recycling via hydrolysis is preferred. This gentle, water-based process breaks the materials down into monomer building blocks without compromising quality.
- Reprocessing
The purified building blocks can then be reintroduced into manufacturing, transforming them back into polymers. This polymer-to-polymer method is both high-yield and energy-efficient, with a significantly smaller carbon footprint than conventional plastic recycling. No permanent microplastics are produced and no fossil raw materials are needed. The materials maintain a quality comparable to that of virgin materials, making them suitable for sensitive applications like food contact.
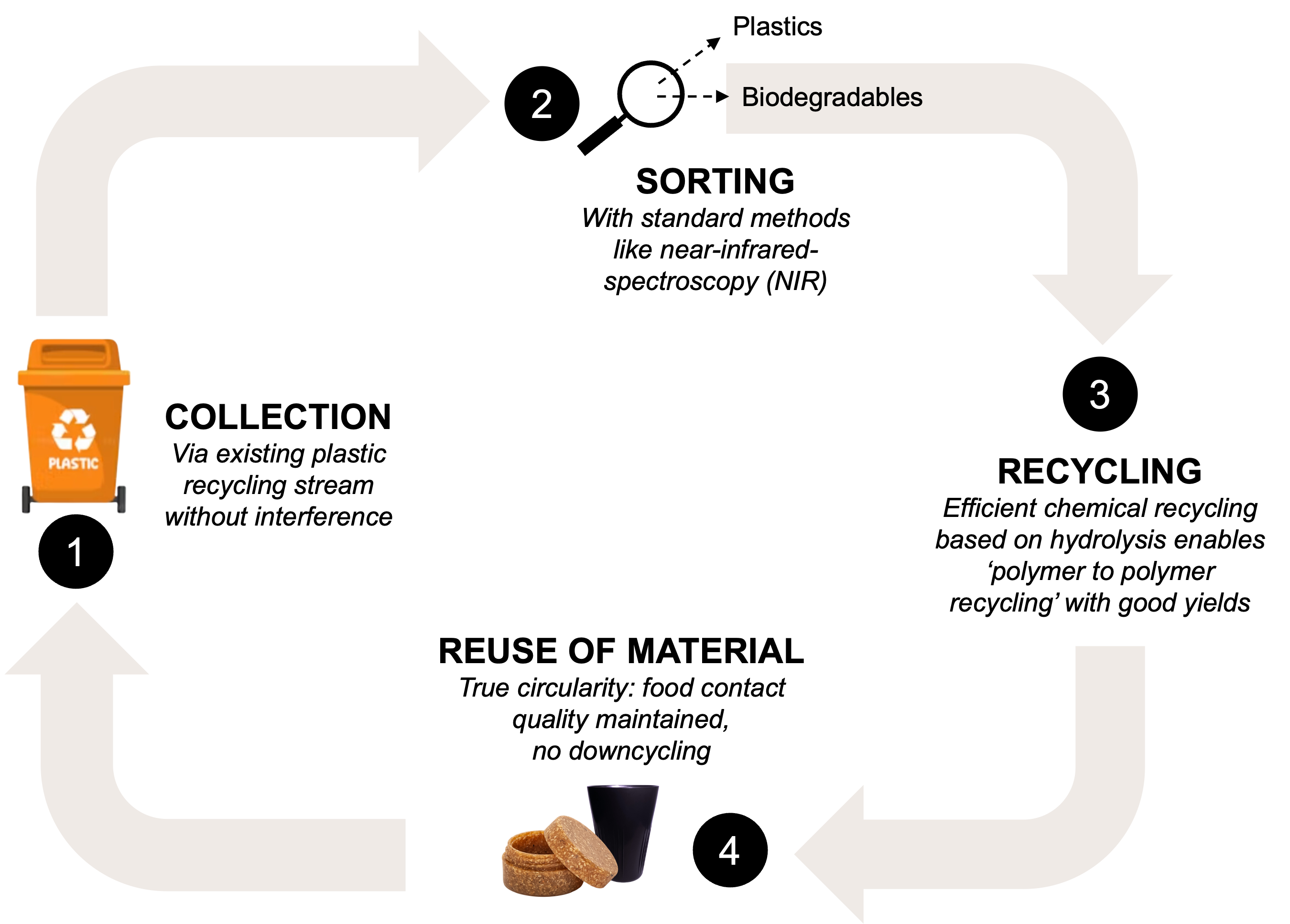
Ecodesign for Sustainable Products Regulation (ESPR)
But wait—there’s more! Alongside the PPWR, the proposed Ecodesign for Sustainable Products Regulation (ESPR) will also impact product standards within the EU. It establishes eco design criteria and introduces a digital product passport to inform consumers about the product’s eco design aspects. Initially targeting electronic appliances, the regulation is expected to expand to all product groups over time.
“For Sulapac, this regulation presents promising opportunities, as it emphasizes the use of sustainable and renewable materials. The goal is to reduce carbon footprints and minimize the release of microplastics into the environment. Since Sulapac materials are biobased and they leave no permanent microplastics behind at any stage of their lifecycle, they align well with the ESPR goals,” Laura says.
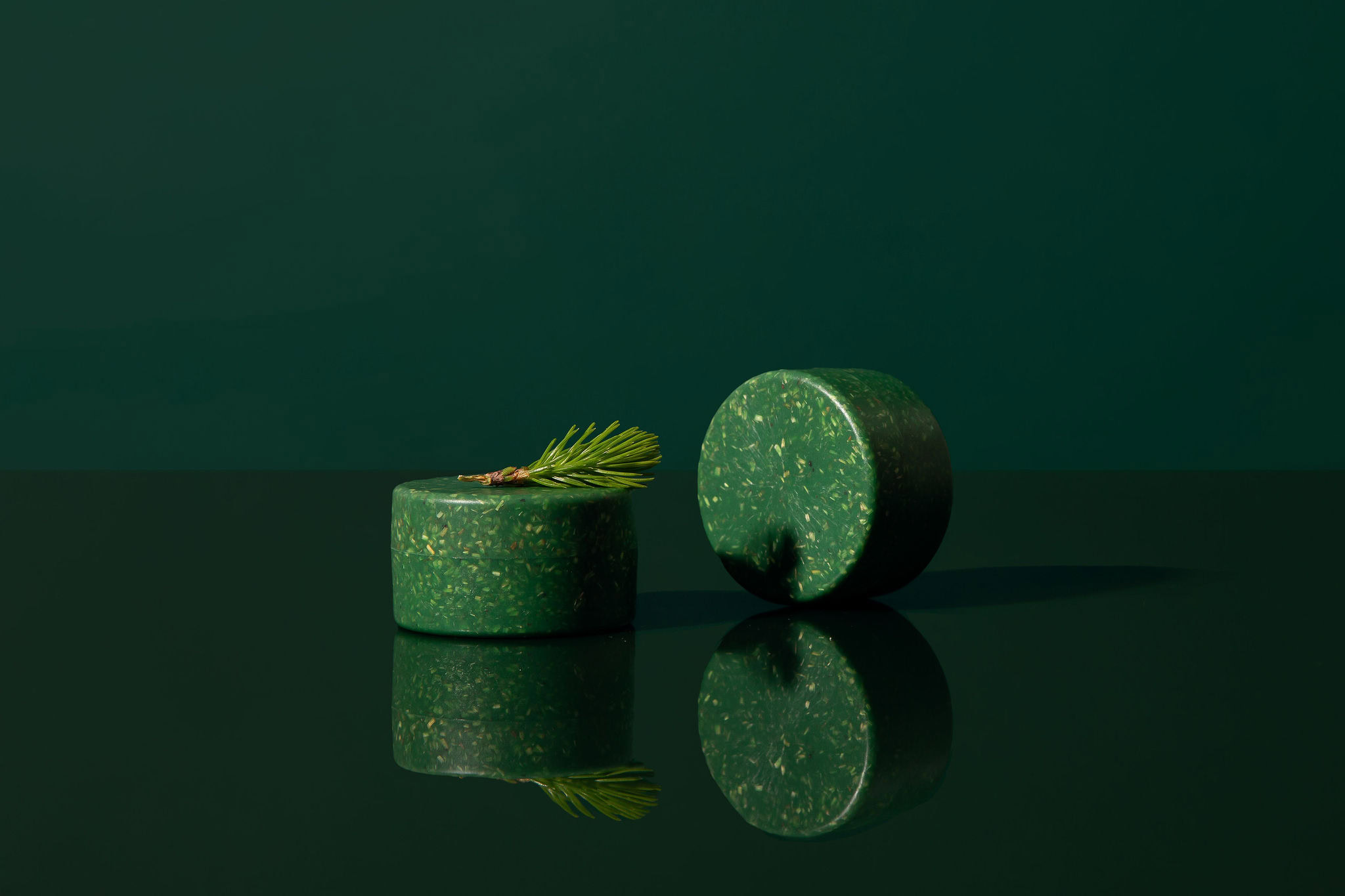
Scaling up the recycling of biodegradable materials
The future looks promising for biobased and biodegradable materials to become recyclable at scale. There is an overall push within the EU to support these materials, which are increasingly recognized as vital solutions for a circular economy. The PPWR mandates EU member states to facilitate the recycling of materials that meet specific recyclability criteria. As the demand for high-quality, and low-carbon, recycled materials increases, the need for chemically recyclable biomaterials is expected to grow. This will lead to more pressure to develop efficient processing and recycling systems.
What does all this mean for your business?
For many businesses, the PPWR may seem like a challenge, but it also represents a significant business opportunity. Consumers are increasingly eco-conscious, and sustainable packaging is a powerful selling point.
Whether you’re in the packaging industry or a business that uses packaging, the time to start preparing for the PPWR is now.
Is your packaging recyclable? Have you considered its ecodesign aspects? If not, what needs to change to ensure it meets the upcoming standards? Proactive steps today can set your business apart. After all, 2030 will be here before we know it.
Would you like to participate in a pilot project? Join us in advancing sustainability through our recycling pilots. Together, we can drive systemic change for a greener future. Contact our experts to find out more!
Sulapac Ltd is an award-winning material innovation company bringing solutions to the global plastic crisis. By replacing conventional plastic with sustainable, beautiful, and functional Sulapac materials, companies can reduce their carbon footprint, eliminate microplastic pollution, and advance the circular economy. The Helsinki-based company was founded by three scientists in 2016 and serves customers across various industries on three continents. Investors behind Sulapac®, the patented material innovation, include CHANEL and Sky Ocean Ventures.