Recycled content – from trash to upcycled treasures
Businesses from different industries are working to increase the proportion of recycled content in packaging – driven by both EU regulation and shifting consumer attitudes. Sulapac turns side stream – and waste-based feedstock into food contact quality material, suitable even for luxury brands. This upcycling means that the material’s value increases when recycled into something beautiful and functional.
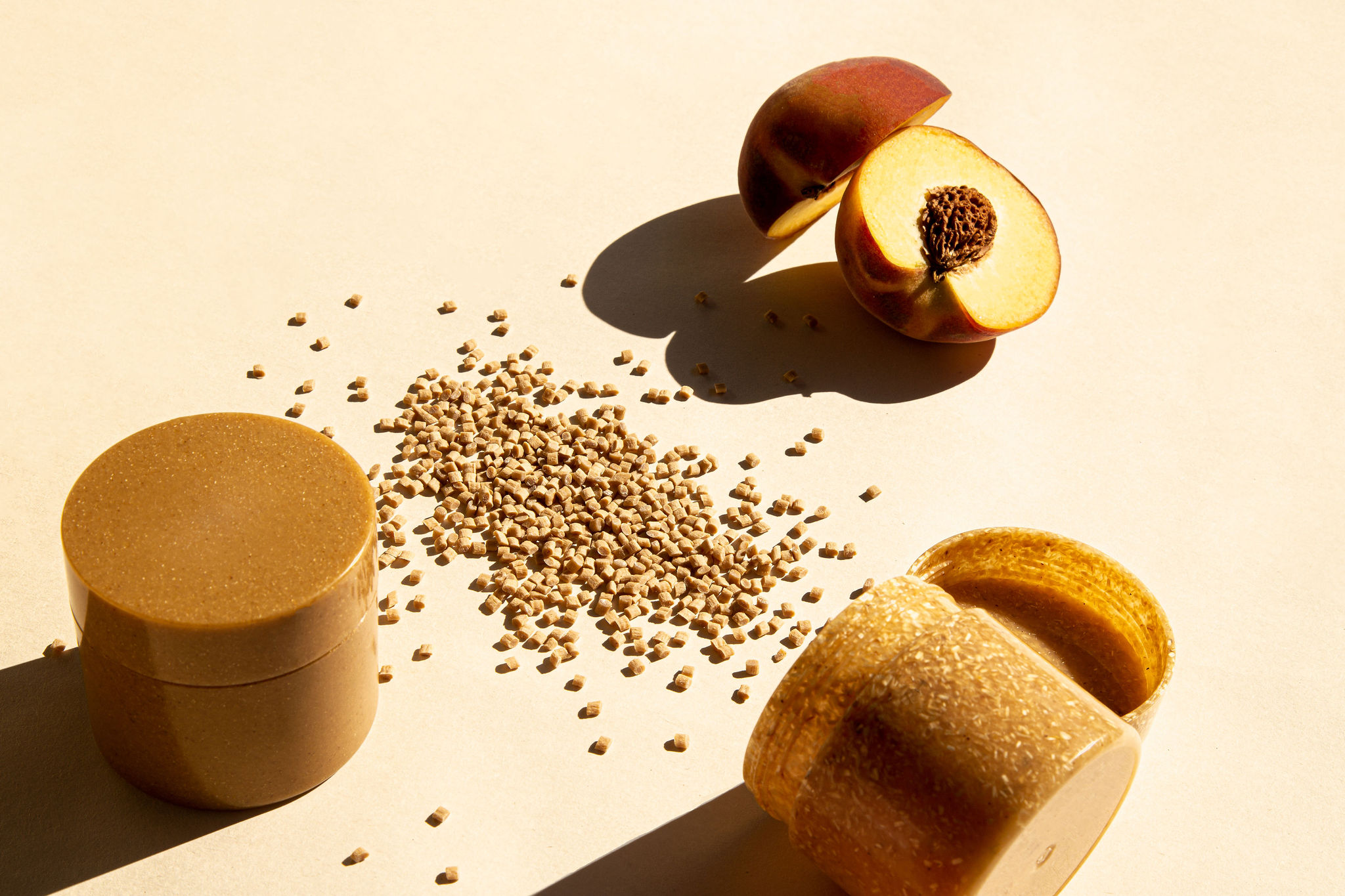
Only recycled content within the next five years
The Packaging and Packaging Waste Regulation, PPWR, aims to ensure that all packaging in the EU is reusable or recyclable in an economically viable way by 2030 (new innovative materials by 2035). This upcoming regulation, along with companies’ internal sustainability targets and consumer attitudes, is pushing businesses to increase the percentage of recycled content they use in their packaging materials.
Sulapac’s ambitious goal is to use 100% recycled or side-stream content within the next five years, when it comes to our main raw materials. Sulapac materials can already be ordered with recycled biopolymers. Currently we can provide materials with up to 70% recycled content in limited quantities and we expect to be able to increase the amount of recycled content, and the maximum quantities available with the highest recycled content year over year. Recycled content has always been part of our recipe, as all the wood material we use is a byproduct of the forest industry.
Defining recycled content
So what is recycled content? As the EU Waste Directive defines it: when a material has been waste or a side stream and can be returned to a usable state, it can be called recycled content. This origin needs to be proven with some suitable method, called chain of custody. At Sulapac we have an internal tracking & verification system at place for recycled content from biodegradable polymers. In addition, we are also initiating the certification process with a global leader in the field of sustainability standards and third-party certification, validation and verification.
The wood we use comes from industrial side streams, but some definitions do not consider it recycled. Hence, when we provide recycled content percentages for our materials, only the recycled biopolymers are taken into account. The total percentage of recycled biopolymers and side stream raw material within a certain Sulapac material is always available upon request.

The different sources of waste
Pre-consumer or post-industrial waste refers to the discarded materials generated during the manufacturing or production process before a product reaches the consumer. Pre-consumer waste typically originates from factories, processing plants, and other industrial facilities and includes materials that do not meet quality standards, production overruns, damaged or defective components, and surplus materials. Pre-consumer waste is often confused with side streams, but they are not the same thing. For example, an incorrect production batch is a form of pre-consumer waste, not a side stream.
Post-consumer means material that has been manufactured into items, used by a consumer, and then disposed of. The material doesn’t become waste until the consumer discards it. Also food waste and used cooking oil from restaurants are a type of post-consumer waste.
Post-consumer waste is classified as third generation feedstock, which means there is no competition with food supply or land use. Third generation feedstock also includes biomass from algae, for example, which then again is not waste. Simple and clear, right?
Feedstock generations of bio-based materials
The classification of bio-based materials into three “generations” is based on the threat they pose to food supply and land use. These terms are not defined by the law or standards, but they are commonly used in research and business. It’s worth noting that the classification into generations is not always strict, and there can be some overlap or variation in the definitions depending on the context and evolving research and technology.
The first-generation feedstocks are usually carbohydrate-rich plants that are also used for food and feed purposes. These feedstocks include crops like corn, sugarcane, wheat, and vegetable oils.
The second generation includes feedstocks that are not suitable for human consumption. They originate from agriculture or forestry as products or side streams. These feedstocks include agricultural residues (such as corn stover, wheat straw), forestry residues (such as wood chips and sawdust), and dedicated energy crops (such as switchgrass and miscanthus). Second-generation feedstocks are considered more sustainable than first-generation feedstocks because they don’t compete with food production.
The third generation feedstocks are derived from non-food sources that do not compete with agricultural land or require arable soil. This group include the most innovative feedstocks, such as some algae, microorganisms, as well as wastes and side streams from the food industry.
Sulapac prioritizes third-generation feedstock in the production of our materials next to the wood chips and wood flour from side streams, which can be classified as second generation feedstock.
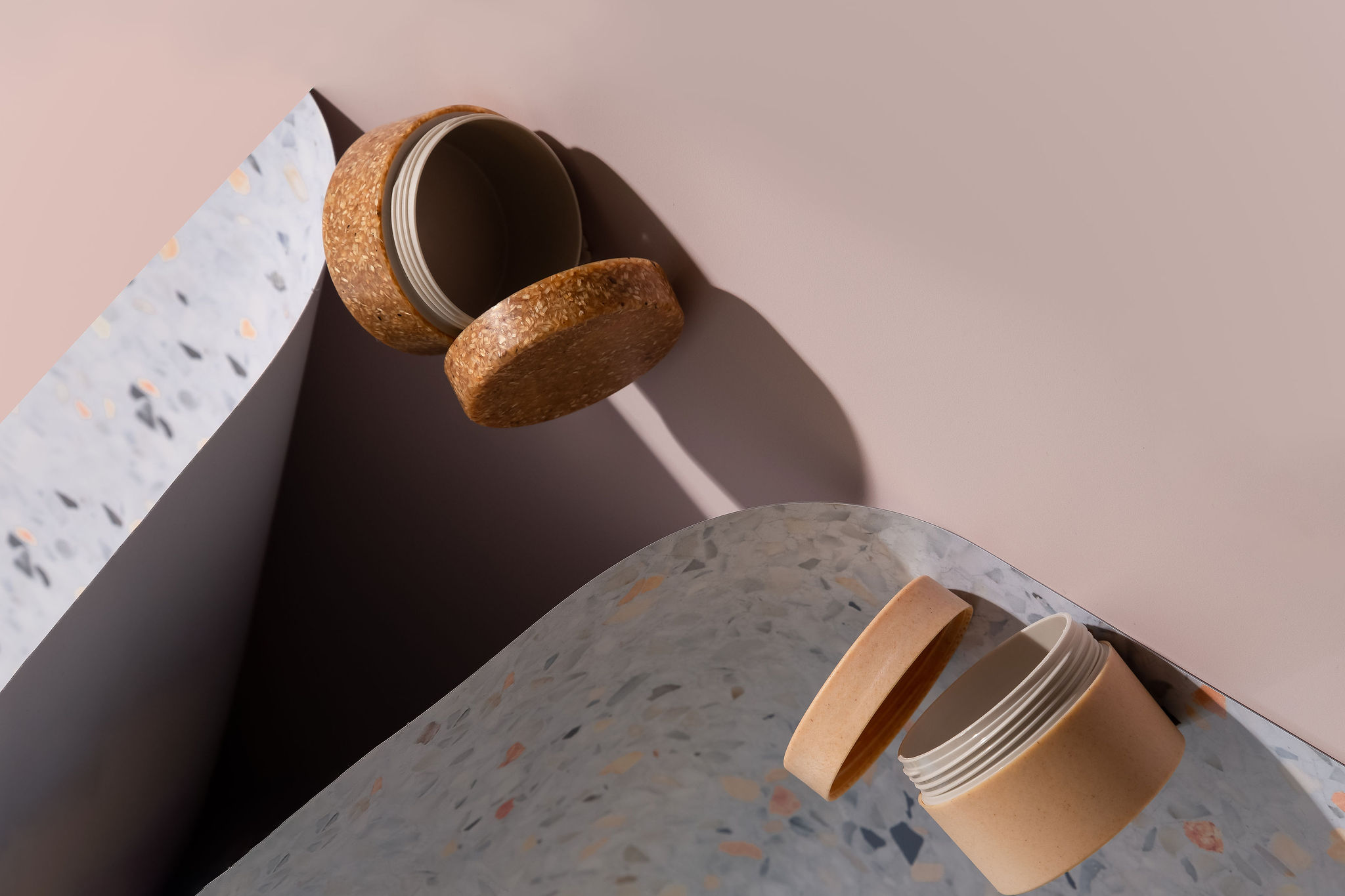
Upcycling increases the material’s value
In terms of mechanical recycling, there are limitations for the use of recycled content as contact material. Recycled oil-based plastic is used, for example, for textiles, packaging, garden items, and construction materials. The recycling of conventional plastic often turns out to be downcycling: the material’s value decreases as it is recycled. Making a reusable bag out of recycled plastic is no longer desirable, as it wastes the value of the material. Besides, how many more shopping bags does the world need?
Sulapac is in the business of upcycling. With upcycling, you increase the material’s value and turn waste into something genuinely useful and valuable. This is where Sulapac’s expertise lies. We transform raw materials originating from side- and waste-streams into beautiful and functional material suitable for food contact. We know how to turn them into material good enough for luxury brands like Chanel and Shiseido. Due to the technology used in the process, the material is as good as a virgin Sulapac material.
What is remarkable is that you don’t have to choose between biobased, biodegradable and recycled content – with Sulapac, you get ’em all.
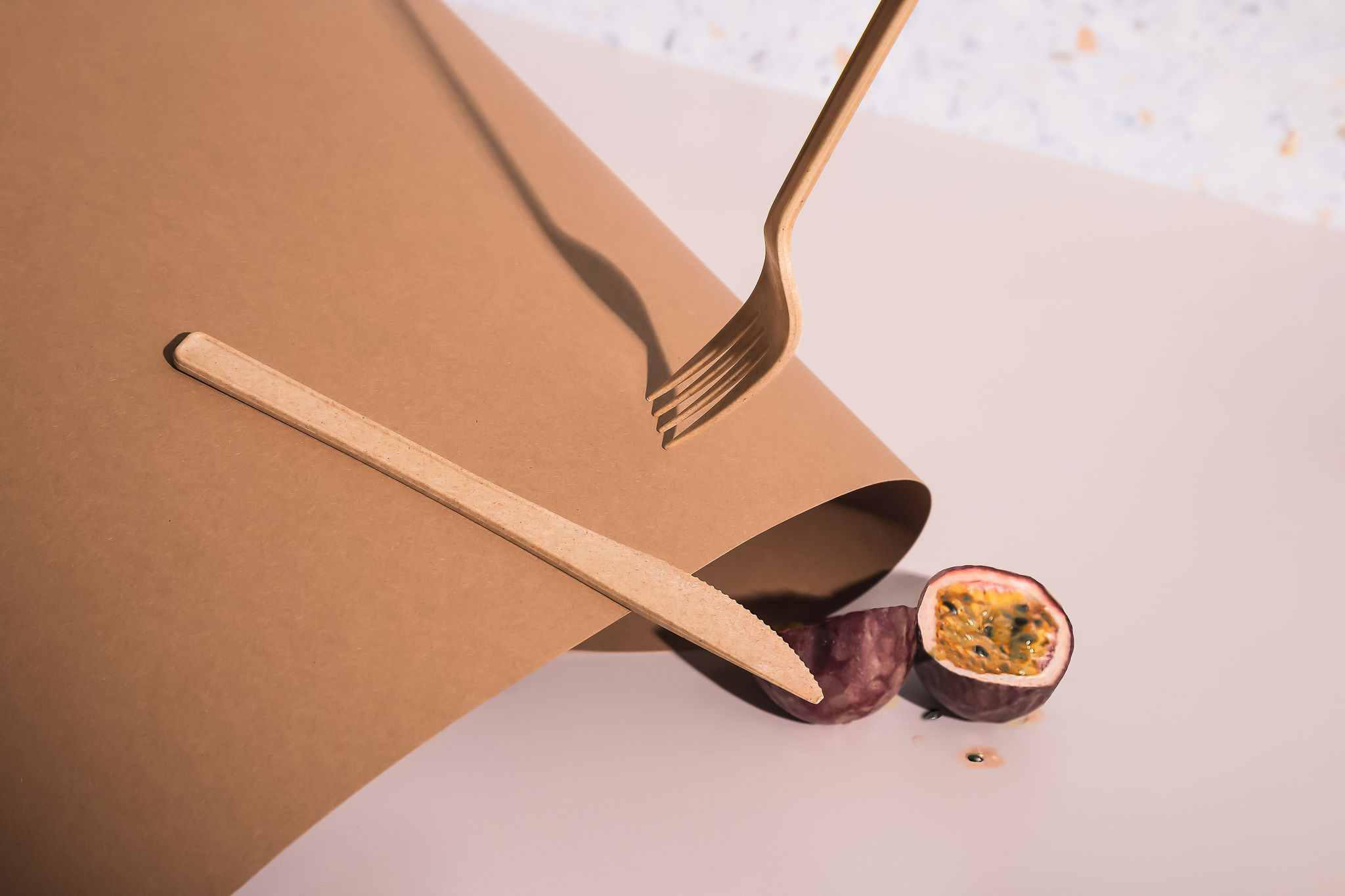
Recycled microplastics are still microplastics
Increasing recycled content while continuing the use of oil-based plastic is not a get-out-of-jail-free card for the disadvantages of plastic. Also recycled plastic releases persistent microplastics. There’s no technology, no trick or compensation method, to change this unfortunate fact.
Rigorous waste management is critical – not only generating less waste in terms of volume but also preventing the harmful effects of the waste. The most efficient way is to replace conventional plastic – recycled or not – with (recycled) bio-based and biodegradable materials, that leave no persistent microplastics or toxic substances behind.
The recycling processes
Recycled plastic mainly originates from the mechanical recycling of industrial side streams and post-consumer packaging waste. Only clean mono materials in developed countries are recycled. Also, only specific polymers are recycled; standard ABS, bakelite, and many others are not. Even when the material is recyclable as such, too small pieces or corroded or dirty materials are rejected in the process. Worldwide, only 9 percent of plastic waste actually gets recycled.
Recycling technologies could be more efficient. Mechanical recycling has a large share of rejection. Chemical recycling of conventional oil-based plastic then again consumes a lot of energy and requires hazardous chemicals. As a comparison, the chemical recycling of bio-based and biodegradable materials is a much more efficient process done under mild conditions which requires less energy and does not require harmful chemicals. Polymer-to-polymer recycling, a type of chemical recycling, means that the material is converted back to into its “building blocks” that can be used again to produce polymers. In chemical recycling the potential contamination of the material entering the process can be resolved with the appropriate controls and processes in place. The purity of the obtained “building blocks” from this process is often similar to the virgin material and can be used to produce food contact-compliant materials. What is more, in polymer-to-polymer recycling the material can circulate almost endlessly without the properties changing.
The treatment of plastic waste is also a significant source of microplastics. A recent case study showed that a single recycling facility can emit an estimated 3 million pounds of microplastics per year. The plastics unsuitable for recycling enter either landfills, where they break down into microscopic pieces leaking into the environment, or the waste is incinerated and the remaining ashes are used for road bases, for example, but the microplastics are still there and continue to spread into the environment.
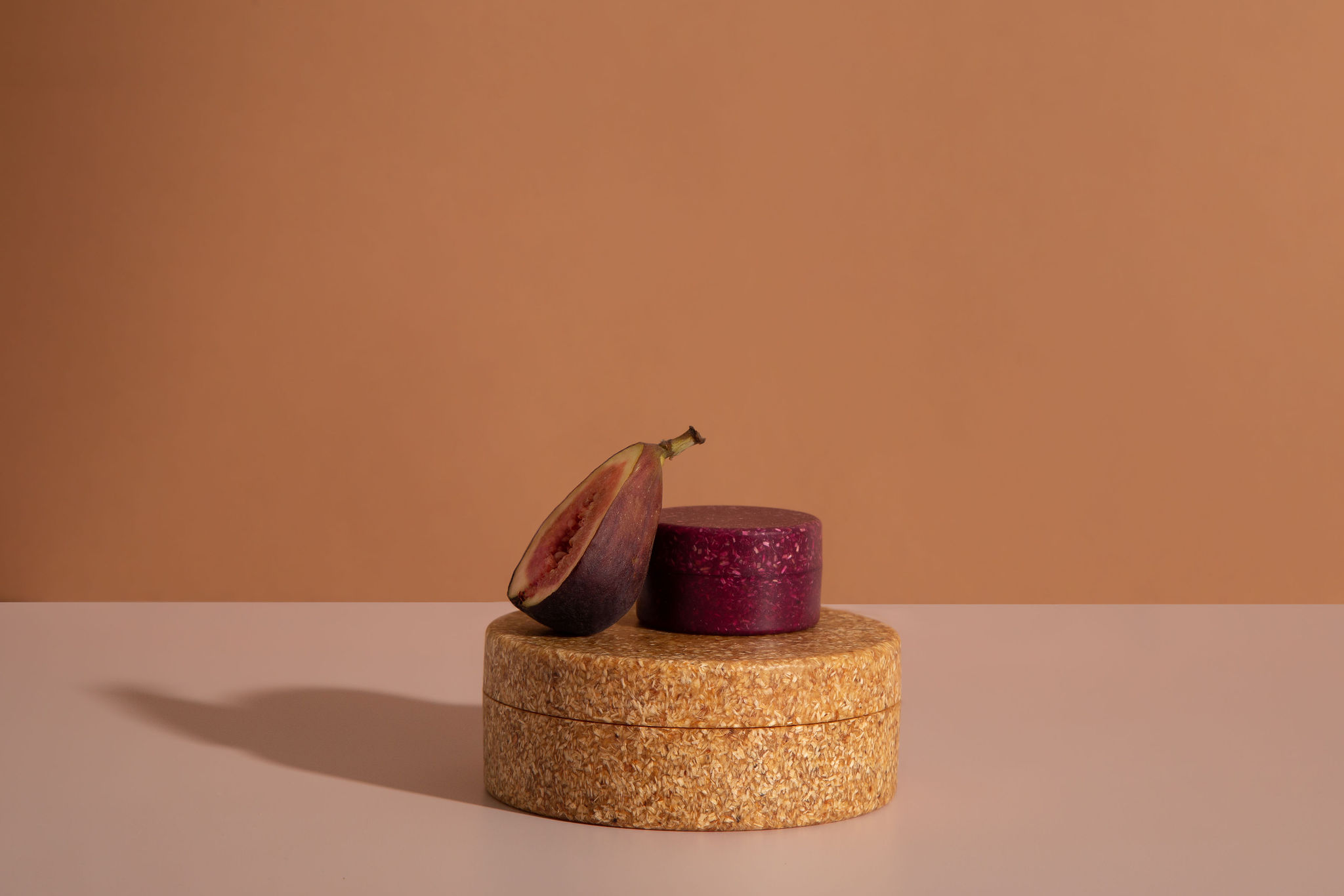
Act now, prepare for future regulation
The demand and curiosity for more sustainable packaging materials among customers are growing. Market demand for recycled content is accelerating the systemic change to circularity. This is the time for forerunners.
It is also smart to already start preparing for future regulation – the PPWR is only a few years away. Not to forget about overall sustainability: recycled content is better for the environment. It reduces negative impacts on climate change and biodiversity. Chemical recycling of polymer-to-polymer is a simple process with significant benefits.
Our goal is to use 100% recycled content (including raw materials from both waste and side streams) by 2025. We know it is an ambitious one, and we are working hard to make it happen. This goal will be reached if the market develops so that enough recycled content is available in the EU. An efficient recycling infrastructure for bio-based and biodegradable materials that works appropriately is a prerequisite. Something we are driving intensively in Finland. Whether the world will follow, is something our customers can impact with their own choices and actions.