The quest for sustainable packaging inserts
Packaging plays a pivotal role in reaching the sustainability and climate goals of fast-moving consumer goods (FMCG) and luxury brands alike. Yet, the shift away from plastic packaging to renewable materials has been painstakingly slow. In this blog, we explore the challenges hindering the transition from plastic to more sustainable packaging alternatives in the context of packaging inserts and present a new solution that has the potential to speed up the change.
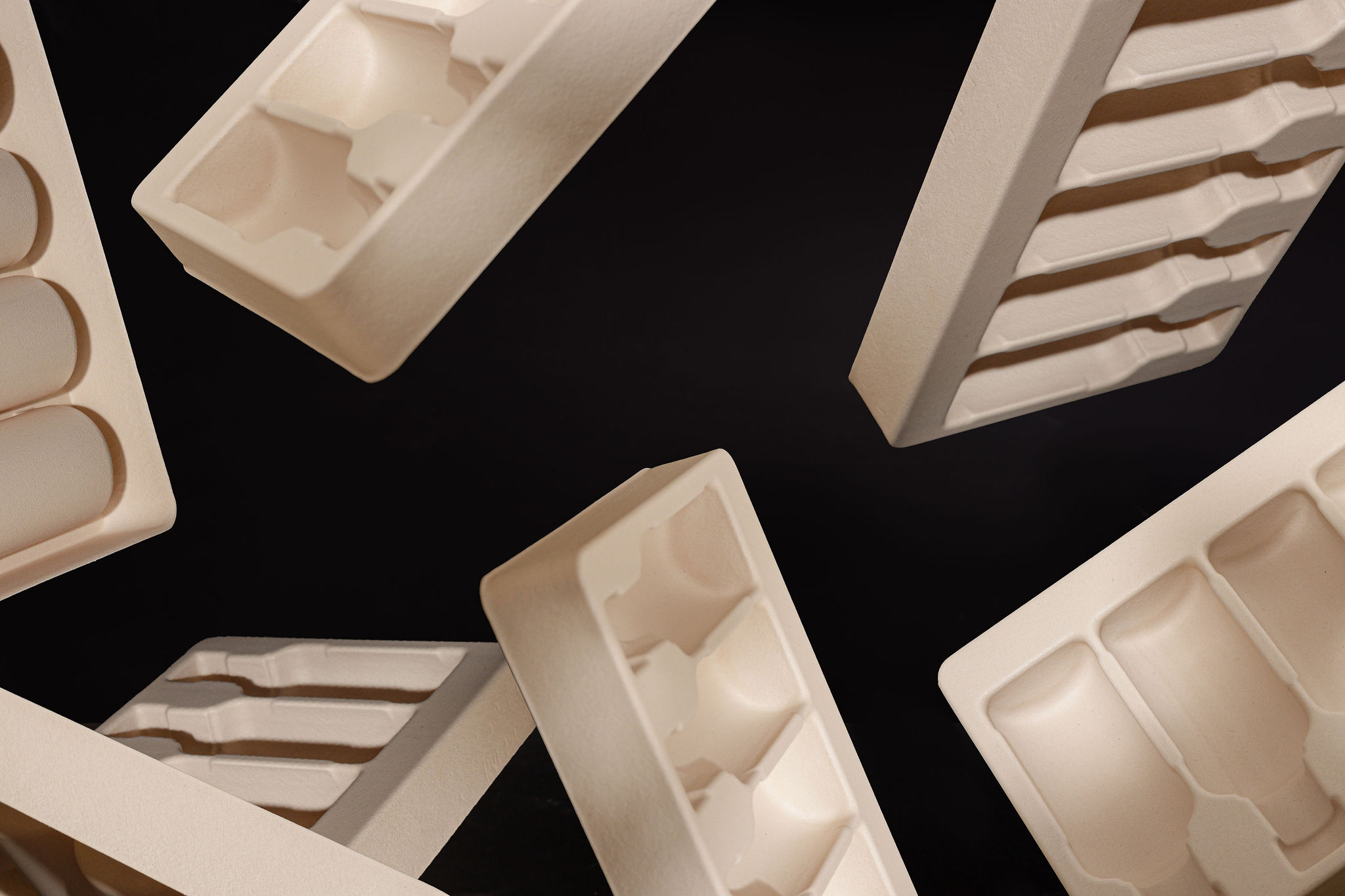
Accelerating the shift towards renewable packaging
Brands across industries, from high-end beverages to luxury cosmetics and familiar bakery goods, are looking for ways to reduce their carbon footprint and the consumption of oil-based plastics. At Sulapac, we are committed to helping brands to achieve these targets in an efficient, hurdle-free manner by offering sustainable material solutions for packaging that fit the existing value chain.
Right now, we are particularly excited about our solution for thermoforming, the Sulapac Flow 1.7 wood-composite material. The material has proven to be the perfect fit for inserts and product trays used to protect and stabilize the product inside secondary packaging or during transportation, offering a truly sustainable, cost-competitive and functional alternative to conventional plastics.
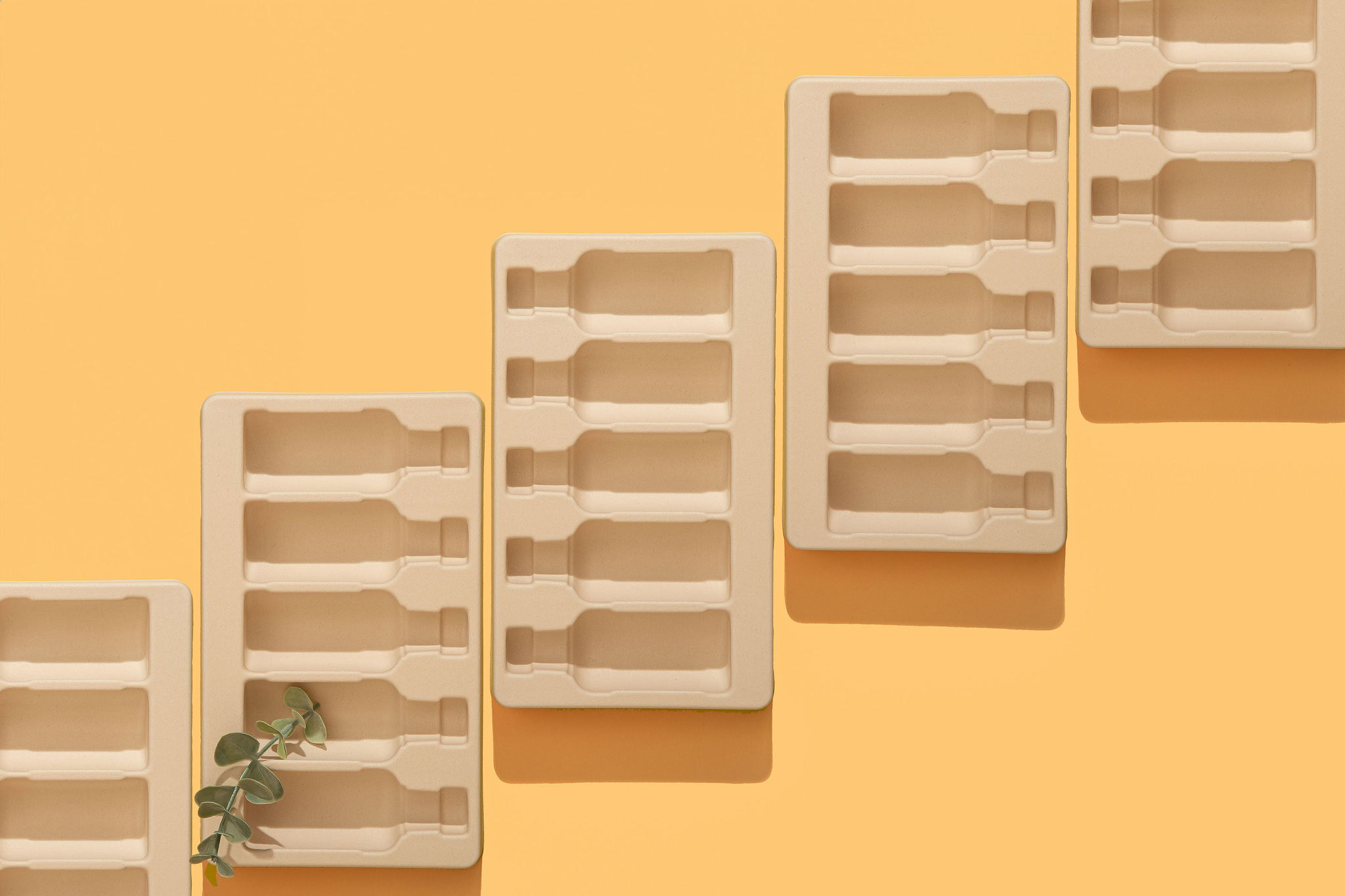
There are also many other sustainable solutions for packaging inserts on the market to replace conventional plastic packaging. However, there are some challenges in adopting them, for example, related to total costs and functionality. Let’s have a look at some of the alternatives to plastic in packaging inserts and the challenges hindering their large-scale adoption.
Cardboard: a renewable option for packaging inserts with limited functionality
As a renewable material cardboard has many sustainability benefits, but there are also certain limitations and challenges that might lessen its appeal as packaging material.
For example, cardboard needs to be folded into shape, which means an additional step in the production process. If you want a design or decoration on your cardboard packaging, the only way to do that is to print it onto the packaging, which again adds another phase to the production process.
Turning wood pulp into cardboard is an energy-intensive process so the carbon footprint is not as low as you would wish. Moreover, especially in food service applications cardboard is often coated with a thin plastic layer, which can make seemingly eco-friendly packaging a source of persistent microplastics and toxic chemicals.
Finally, cardboard recycling isn’t as effective as often thought. Typically, cardboard gets downcycled into lower-quality products until it gets disposed of, because the fibers become shorter and weaker with each recycling cycle, meaning the quality and usefulness of the material is reduced. On average cardboard can be recycled around five to seven times.
Formed fiber: packaging without a ‘memory’
Unlike cardboard, formed fiber packaging is ready to use right out of production, eliminating the need for the folding and assembly required with cardboard inserts.
Unlike cardboard packaging, formed fiber packaging can be molded to the exact shape of the product it is designed to protect, providing better support compared to folded cardboard inserts which may not fit as snugly.
However, formed fiber packaging has no ‘memory’. In other words, mechanical stress breaks the fibers, and the insert won’t bounce back to its original form once the product has been removed. Thus, the product can’t be clicked in and out repeatedly which limits the application possibilities of formed fiber packaging.
Compared to cardboard, formed fiber packaging can be considered a more high-quality solution with the possibility to incorporate designs, logos, and textures that can enhance the unboxing experience. Yet, one of the most common formed fiber applications is egg carton, indicating that this is perhaps not the most desired option in the luxury categories.
Injected pulp: premium packaging solution with high costs
Pulp injection manufacturing utilizes high-pressure injection to create precise shapes with high consistency and level of detail. This makes injected pulp suitable for more complex, upscale applications such as electronic product packaging.
One of the downsides of this packaging solution is the extremely high setup cost, as the injection process requires sophisticated machinery. The price of a single mold ranges from $10,000 to $100,000.
In terms of recycling, both injected pulp and formed fiber packaging suffer from the same fiber degradation issues as cardboard. While they can be recycled, the number of cycles is limited (typically around five to seven times), after which the material is downcycled into lower-quality products until it can no longer be recycled and must be disposed of.
PLA: sustainable material with suboptimal processability
PLA is a sustainable option for conventional plastics that can be used in existing thermoforming product lines. However, based on the information that we have received from the field, its processability is not as good as one would hope, which makes it a less of an appealing option. Furthermore, PLA has a narrower processing window comparing to conventional plastic, which means it requires more precise temperature control during thermoforming.
rPET: the non-renewable option for virgin plastic in thermoforming
Recycled PET has a lower carbon footprint compared to virgin plastic and it has a positive environmental impact in a sense that it reduces the need for resource extraction, albeit only in a limited manner.
As PET is recycled, the quality of the material degrades in each cycle, so rPET may be weaker than virgin PET, which is typically treated by mixing recycled PET with virgin PET.
Besides the continued need for oil, rPET may have additional environmental disadvantages, i.e. ecotoxic impacts, that we touched upon in our recent blog Is recycled PET really the best you can do.
Finally, the processability of rPET in thermoforming is not on a same level as that of virgin plastic, due to its lower intrinsic viscosity and potential for increased brittleness.
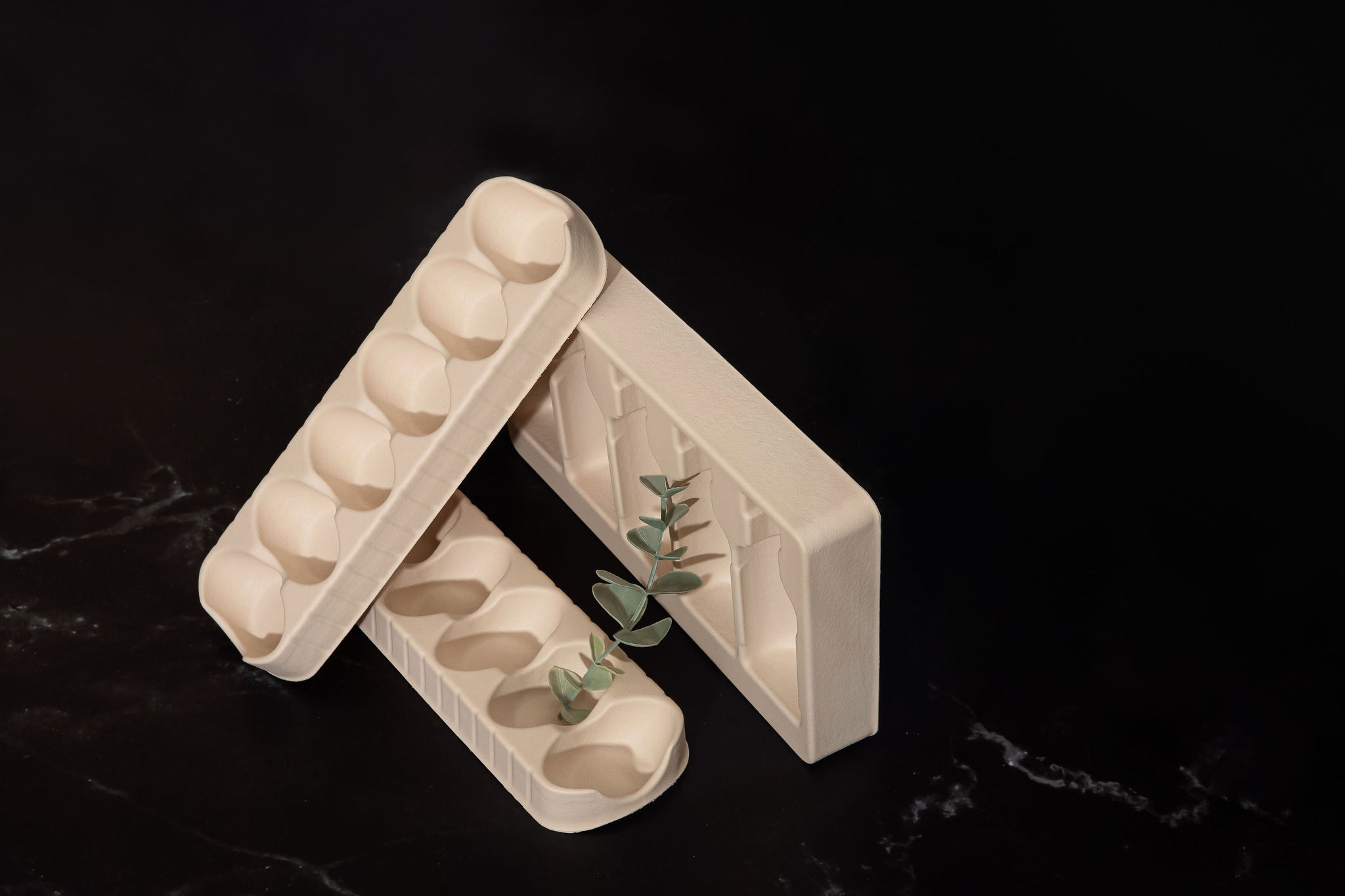
Sulapac Flow 1.7: the benefits of plastic without the environmental burden
Sulapac Flow 1.7 is a sustainable wood composite that provides an eco-friendly and practical solution for thermoformed packaging inserts without sacrificing quality or functionality.
It is fast and easy to process and has gained extremely positive feedback from thermoformers across Central Europe and the US. The consistency of the material ensures stable production with minimized scrap and machine downtime. Sulapac Flow 1.7 is often used to replace polystyrene, and the great news is that manufacturers have managed to reach a similar processing speed with Flow 1.7 as with PS.
Sulapac Flow 1.7 has a ‘memory’, just like conventional plastic, which means you can click your product in and out repeatedly. Furthermore, Sulapac Flow 1.7 allows for detailed surface structures with high precision and is available in your brand color. What is more, the pleasant, natural look and feel eliminates the need for flocking.
Sulapac Flow 1.7 allows brands to switch from conventional plastic packaging to a more sustainable solution with minimal effort: you can continue working with the same manufacturer and with the same equipment, just ask your thermoforming partner to order Sulapac® rolls or sheets instead of the old-school plastic ones.
The environmental benefits of Sulapac Flow 1.7 are indisputable: reduced CO2 emissions, no permanent microplastics, no PFAS, no ecotoxic effects.
Sulapac materials can be separated from the mixed waste stream with standardized technologies like NIR, so packaging made of Sulapac Flow 1.7 can be disposed of with plastic waste. The material is recyclable both mechanically or in a highly efficient chemical recycling process based on hydrolysis. Waste management companies will start processing Sulapac and other biodegradable materials once the volumes grow. There is also an option for closed-loop waste collection and recycling organized by Sulapac.
Sulapac Flow 1.7 is certified industrially compostable, so composting is a potential end-of-life option for certain applications as well.
Please, ask for more details from your Sulapac account executive!
Sulapac Ltd is an award-winning material innovation company bringing solutions to the global plastic crisis. By replacing conventional plastic with sustainable, beautiful, and functional Sulapac materials, companies can reduce their carbon footprint, eliminate microplastic pollution, and advance the circular economy. The Helsinki-based company was founded by three scientists in 2016 and serves customers across various industries on three continents. Investors behind Sulapac®, the patented material innovation, include CHANEL and Sky Ocean Ventures.