How to get your thermoforming production flowing with biodegradable Sulapac Flow 1.7
Thermoforming has traditionally relied on conventional plastic, a major contributor to global greenhouse gas emissions and a source of microplastic pollution. As the push for sustainability and greener alternatives intensifies, thermoforming manufacturers are seeking materials that are both eco-friendly and easy to process. Enter Sulapac Flow 1.7 – a bio-based and biodegradable thermoforming material that not only makes stunning products but is also just as easy to work with as conventional plastic.
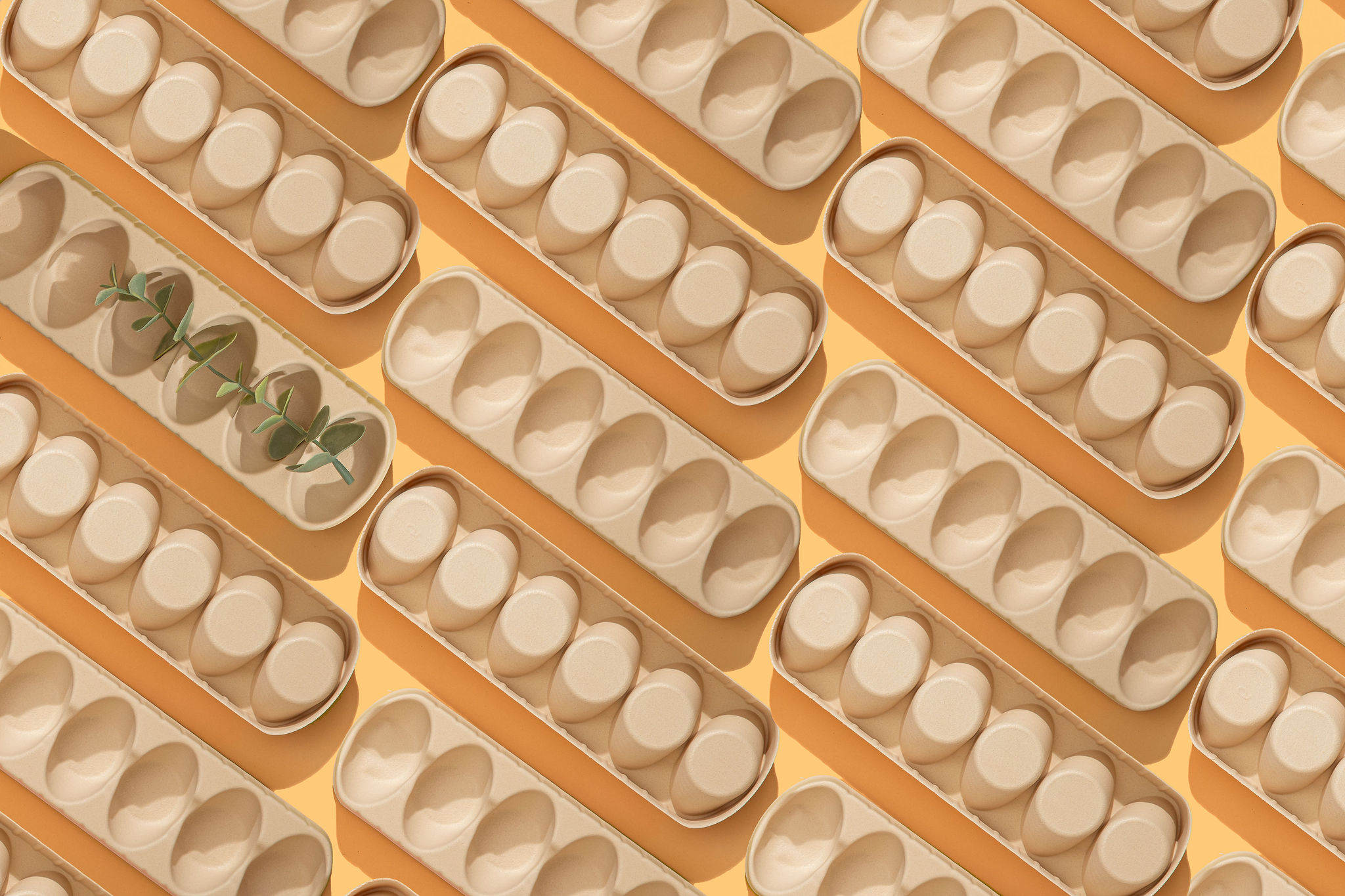
Thermoforming is a manufacturing process that involves heating a plastic sheet and shaping it into a specific form using a mold. It’s a cost-effective and versatile method that allows for quick prototyping and high-speed production, making it one of the most common manufacturing processes across several industries. Thermoforming is especially suited for high-volume production of simple shapes such as packaging inserts, cups, and food packaging.
A significant and pressing challenge in thermoforming is replacing plastic materials, which contribute to microplastic pollution, with sustainable alternatives – while retaining the many benefits of plastic.
Sulapac Flow 1.7 – a bio-based, biodegradable, and recyclable option
Sulapac Flow 1.7 offers the best of plastic without burdening the environment. Its main components are biodegradable biopolymers as well as sawdust and small wood chips – residues from wood processing that would otherwise be burned. The material can be both chemically and mechanically recycled.
Sulapac Flow 1.7 is ideal for producing sustainable packaging inserts and product trays designed to stabilize and protect items inside secondary packaging or during transportation. It also works well in retail displays, drinking cups and lids, food containers, and cake trays, just to name a few.
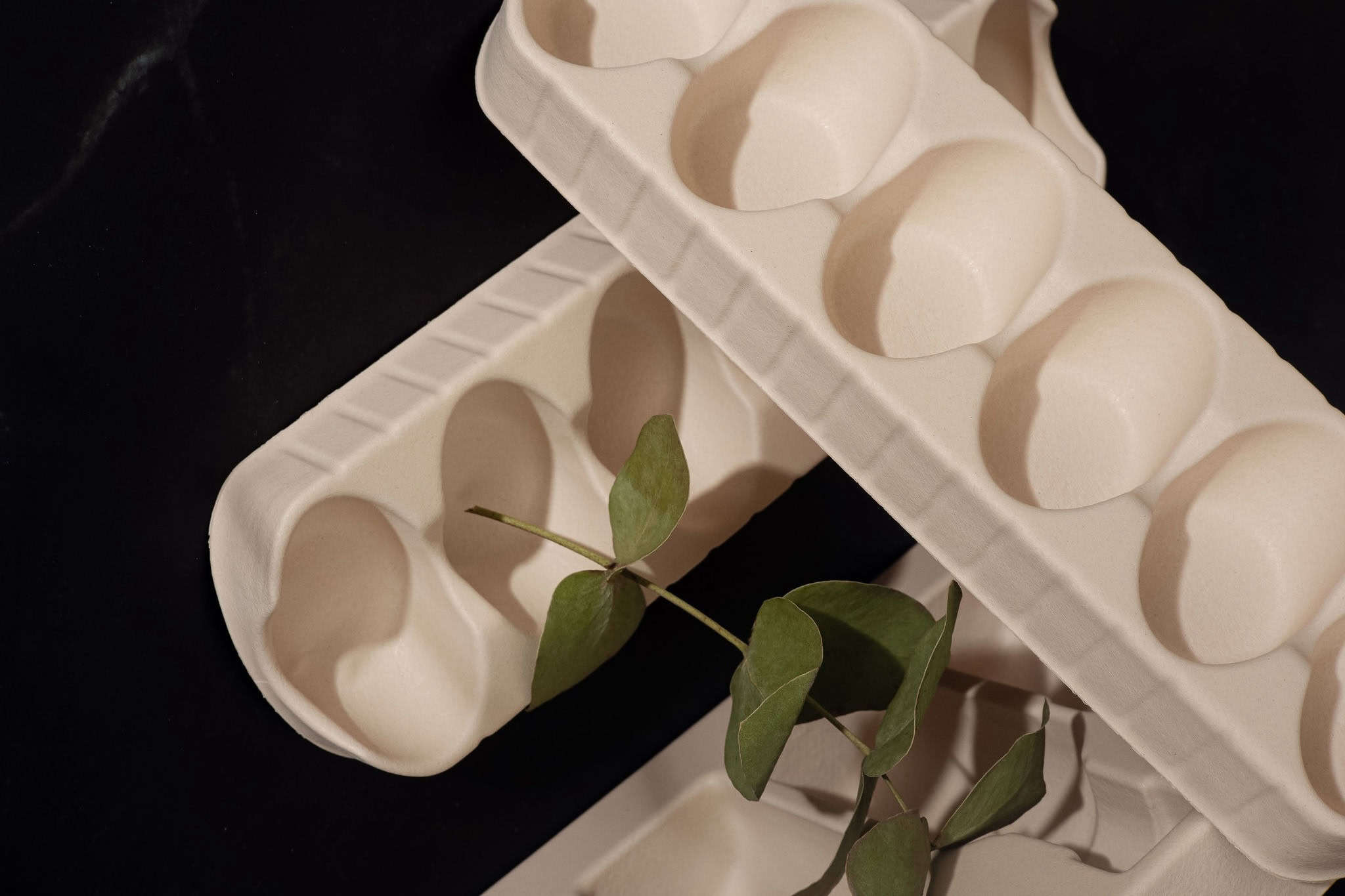
There’s a new thermoforming material on the block
Feedback from industry professionals at recent trade shows has been enthusiastic.
“Many people we’ve talked to have mentioned that the new thermoforming materials they’ve come across in the past years have mostly been recycled PET or various technical plastics. They’ve remarked that our Flow 1.7 material is the first truly innovative development in thermoforming in decades,” says Joona Kontinen, Growth & Innovations Manager at Sulapac.
There are, of course, some sustainable alternatives to conventional plastic on the market, but their large-scale adoption is often hindered by various challenges.
Unlike many other sustainable thermoforming materials, Sulapac Flow 1.7 combines the best of both worlds – the high performance, affordability, and excellent processability of plastic and the environmental advantages of sustainable materials, such as formed fiber or cardboard.
“Customers with prior experience using sustainable materials may have concerns about quality consistency. But once they see the products made with Flow 1.7 and actually get to try the material themselves, the feedback we keep receiving has been phenomenal,” Joona continues.
“We’re absolutely delighted to be working with Sulapac on this exciting new project. We’ve trialled the material, and I must say this is the first time that we’ve come across a sustainable alternative to conventional plastic that actually works! It ticks all the boxes, and our customers’ response has been terrific. The material is really easy to use. Conventional tooling is fine for this material, and our machines need very little adjustment in order to run it.”
– Richard Moor, Director, Thomas Ellis Engineering
Incredibly easy to work with
Sulapac Flow 1.7 features all the versatility and processability of plastic – such as the ability to imprint patterns or text directly onto the molded product.
“The material is just as easy to use as conventional plastic. Just load it into the machine, and you’re ready to start production with no additional steps needed. Our customers have been thrilled that they can start production and then just take a coffee break and let the machine do its thing,” Joona explains.
He recalls an amusing incident. “Once, I suggested to a client that we should have a technical call before they start thermoforming. Within three minutes, they sent back pictures of what they had already made – quite complex pieces that impressed even me. So, no call was needed,” Joona laughs.
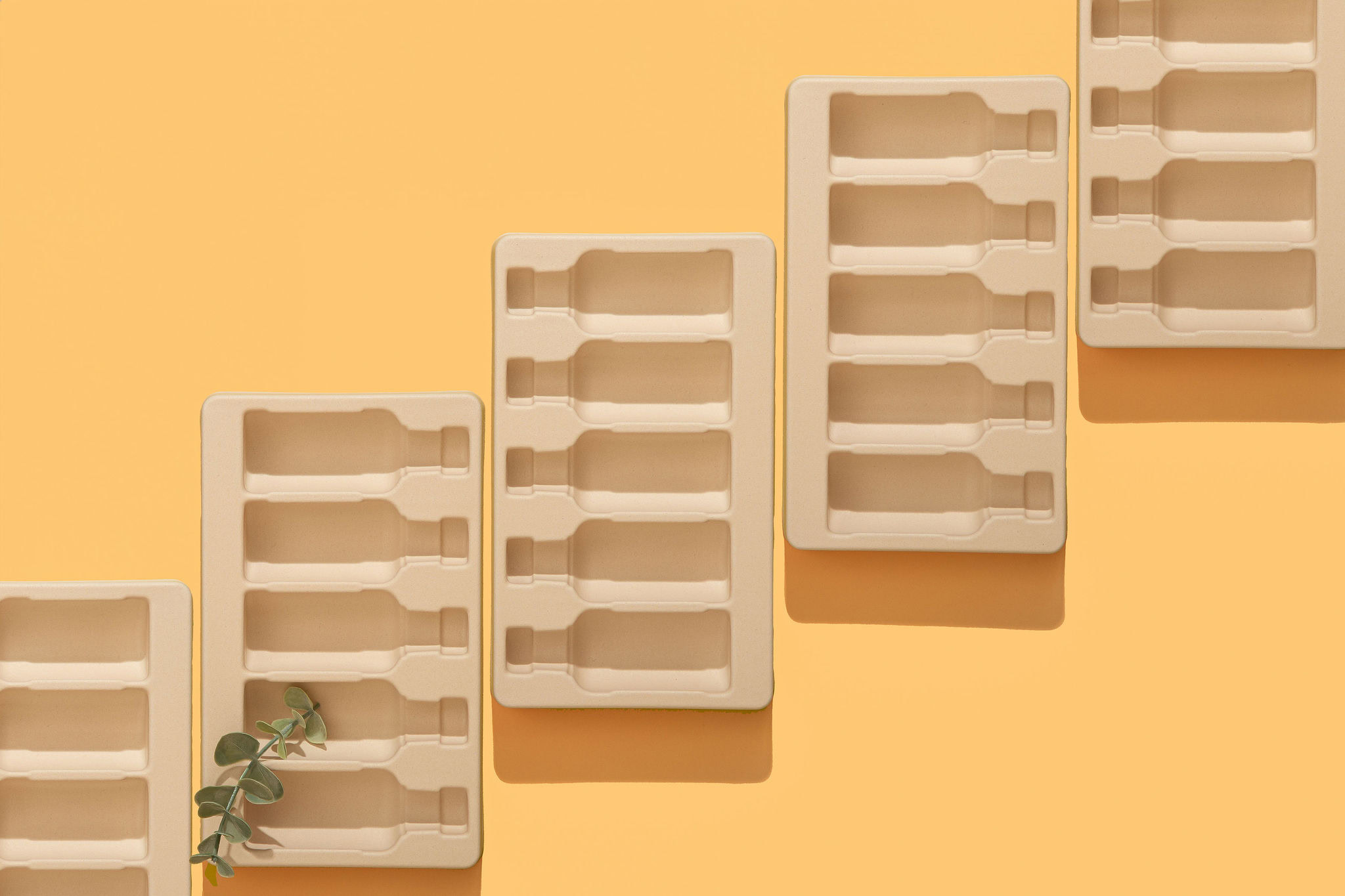
Less heating, more efficiency
Sulapac Flow 1.7 requires lower temperatures for thermoforming than conventional plastic, leading to significant energy savings.
“Based on our clients’ experiences so far, our material can deliver from 5% to 20% energy savings by reducing heating time. Since less heating is needed, it can also speed up production by up to 20 %, compared to conventional plastic. This makes it a very competitive solution and balances out the slightly higher price,” Joona says.
Seamlessly integrates into your production process
Sulapac Flow 1.7 seamlessly integrates into both inline production lines and processes where sheets are formed separately. It is well suited for both light and heavy gauge applications.
Additionally, it’s a drop-in solution. You can simply swap your existing material without having to invest in new equipment.
During tests conducted in various inline production lines, the transition from polystyrene to Sulapac Flow 1.7 has been smooth. Only minimal adjustments to extrusion and forming temperatures have been necessary – routine tweaks that are often needed anyway.
The material performs almost like conventional plastic, running efficiently through processes like lip rolling without sticking. Production speeds match those of polystyrene, and existing robotic systems with suction cups function effectively with the material. Leftover skeletons can also be fully recycled back into production.
In processes where sheets are produced separately and later thermoformed, Sulapac Flow 1.7 has proven effective in both vacuum and pressure forming. In sheet extrusion, no post-treatment with silicone is needed.
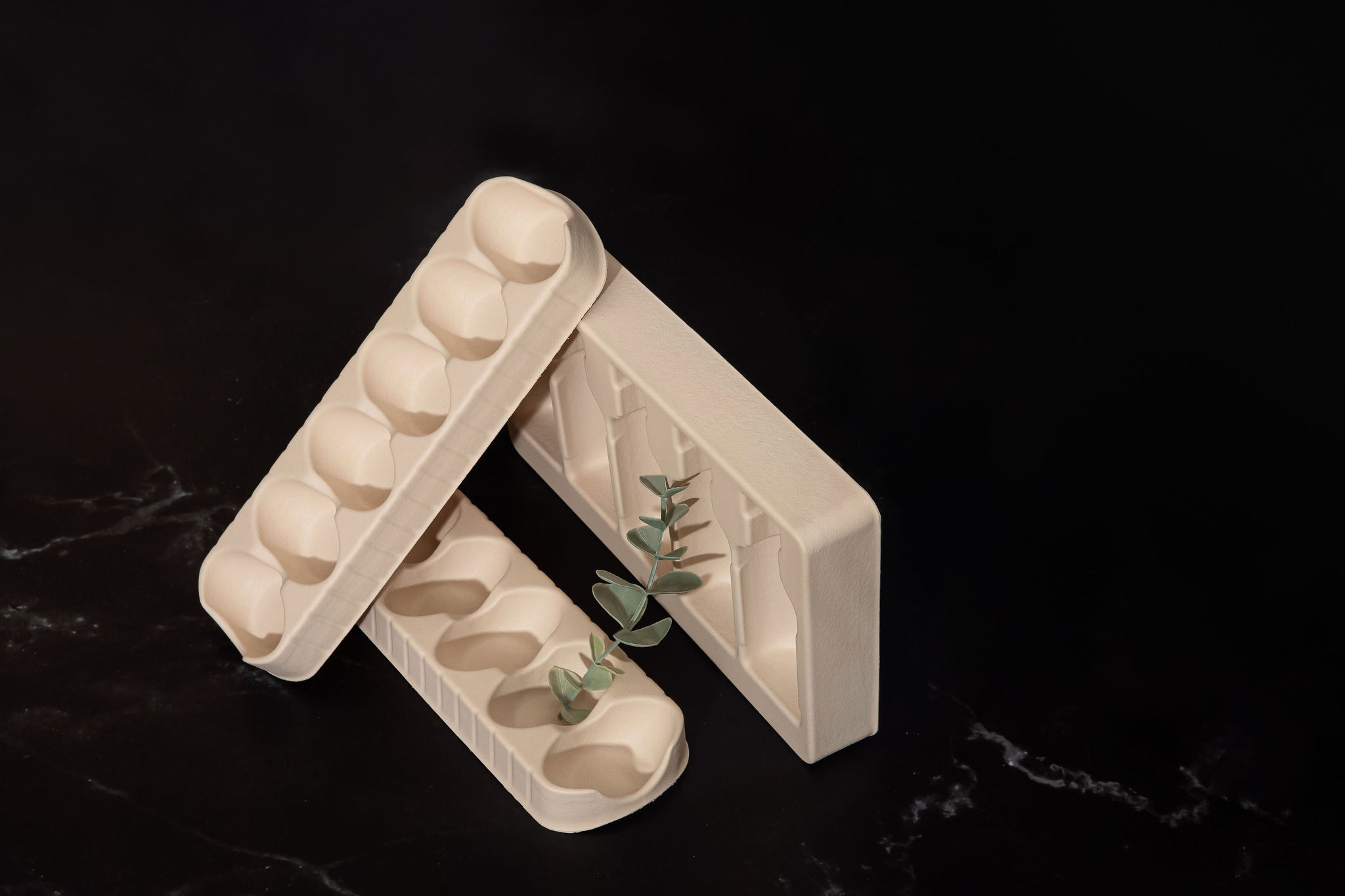
Performs like plastic, but doesn’t look like it
When producing plastic packaging materials, there’s also the aesthetic side to consider. And plastic will always look, well, like plastic.
The unique texture and feel of Sulapac Flow 1.7 set it apart from conventional plastics. Premium brands, in particular, often prefer to use packaging inserts that convey a luxurious look and feel. That’s why they frequently enhance the appearance of plastic inserts with a leather- or suede-like finish.
However, with Sulapac Flow 1.7, there’s no need for flocking or other post-treatments. “Many brands have remarked that our material looks impressive as it is and prefer not to cover it up. This reduces costs by eliminating an additional step in the production process. Additionally, the material can be dyed in virtually any color, allowing for a high level of customization and detail,” Joona explains.
Stay one step ahead with bio-based and biodegradable thermoforming materials
With the new Packaging and Packaging Waste Regulation (PPWR) and the Eco design requirements set to take effect in the near future, thermoforming manufacturers can stay ahead by swiftly adopting biobased, biodegradable, and recyclable materials. The regulation aims to increase the recyclability of packaging materials and the use of recycled content, as well as restrict the use of single-use plastics. The European Parliament now acknowledges that packaging made with biodegradable polymers can also be recycled.
By using recyclable materials consisting of biobased and biodegradable polymers, thermoforming manufacturers can decrease the use of fossil feedstocks and ensure that their products don’t release permanent microplastics into the environment.
All in all, the future looks exceptionally bright for Sulapac Flow 1.7. “It’s already a very versatile material, but ongoing innovations are set to broaden its applications further. By choosing biodegradable materials, manufacturers can take a proactive role in the transition towards a more sustainable future,” Joona says.
Want to make a smooth switch from conventional plastic to a beautiful and sustainable thermoforming material? Please don’t hesitate to contact our experts – they’ll be more than happy to help you!